Overview:
Plastic injection molding for plastic bottle covers is a highly efficient manufacturing process used to produce durable, precise, and customizable bottle caps or covers. This technique allows for the creation of intricate designs and uniformity in large volumes, making it ideal for industries requiring consistent quality and cost-effectiveness. The advantages of plastic injection molding in producing bottle covers include fast production speeds, high precision in size and shape, and the ability to use a variety of materials for enhanced durability. We offer fully customizable services, allowing you to choose the size, color, and even add custom logo printing to meet your unique requirements. At our factory, we specialize in delivering high-quality, tailored plastic bottle covers that align with your brand and product specifications.
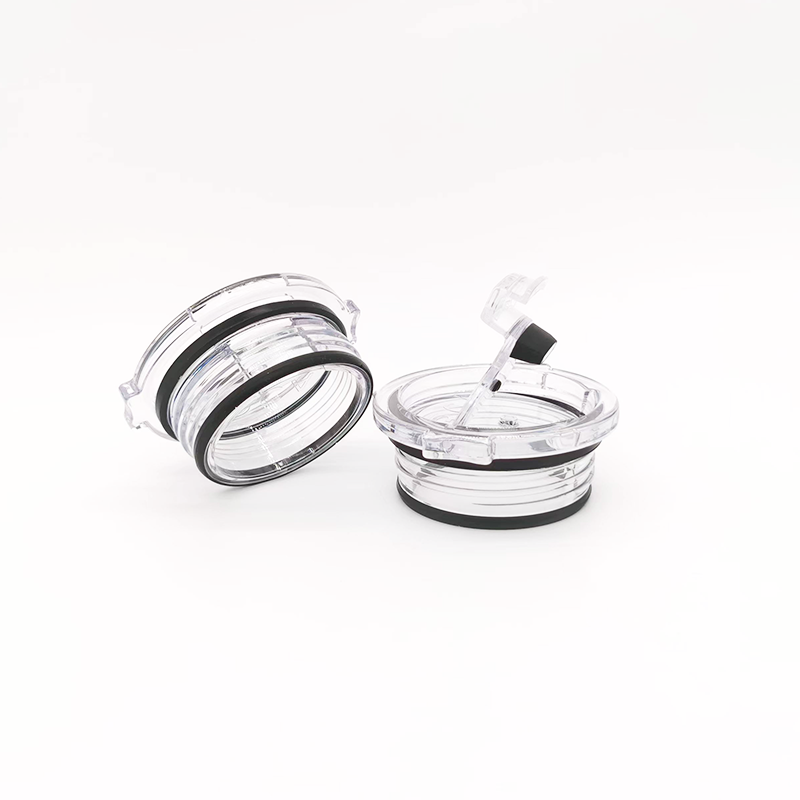
Characteristics:
Attribute | Details |
Place of Origin | Xiamen, China |
Custom Order | Accepted |
Brand Name | OEM |
Color | Customized Color |
Size | Custom |
Application | Bottles, Cups |
MOQ | According to your requirement |
OEM | Accepted |
Material | PP Plastic |
Logo | Custom Logo |
Colors | Custom |
Process Technology | Plastic Injection Molding |
Advantages of Our Covers:
- High Precision and Uniformity in Production
- Cost-Effectiveness for Large-Scale Manufacturing
- Design Flexibility for Custom Shapes and Features
- Material Efficiency and Sustainable Manufacturing
Manufacturing Process:
- Material Selection and Preparation
The process begins with selecting the appropriate plastic material, typically polypropylene (PP), based on its durability, flexibility, and cost-effectiveness. The raw plastic is then fed into a hopper, where it is preheated to the optimal molding temperature for injection.
- Injection Molding
The preheated plastic material is injected under high pressure into a custom-designed mold cavity. This step ensures the plastic takes the shape of the bottle cover, filling the cavity completely and forming an even, detailed shape.
- Cooling and Solidification
After the material is injected into the mold, it is cooled rapidly using a water-cooling system. This cooling process solidifies the plastic, giving the bottle cover its final shape and size.
- Mold Opening and Ejection
Once the plastic has cooled and solidified, the mold opens, and the newly formed plastic bottle cover is ejected from the mold cavity using automated ejector pins or other mechanisms.
- Quality Control and Inspection
Each plastic bottle cover is thoroughly inspected for any defects such as warping, bubbles, or dimensional inaccuracies. This step ensures that the final product meets the required specifications for functionality and aesthetics.
- Finishing Touches (Optional)
Additional processes like trimming excess plastic, adding color, applying logos, or printing designs can be done during or after molding to meet customer requirements.
- Packaging and Shipping
Finally, the plastic bottle covers are carefully packaged for transport, ensuring they remain undamaged during shipping and ready for assembly or direct use.
Factory Show:
Our facility is equipped with advanced machinery, including CNC machines, Mirror EDM, EDM, and Slow-speed Wire Cut (WC) for precision mold-making. We operate 15 rubber compression machines and 2 LSR injection molding machines.
For quality assurance, we use 3D projectors, sealing testers, durometers, and employ CMM inspections along with a qualified QC team.
Our production also includes automated screen printing, high-speed doming, and die-cutting machines. With a focus on quality control and compliance with ISO 9001 and IATF 16949 standards, we ensure top-tier product quality throughout the manufacturing process.