Overview:
Metal battery terminal connectors are essential components that link batteries to electrical circuits, ensuring reliable power flow. Made from high-conductivity metals like copper, brass, or aluminum, these connectors are often coated to prevent corrosion. They are produced through stamping, casting, or forging, followed by precision machining. We offer custom battery terminal connectors in various sizes and specifications, backed by advanced production equipment and rigorous quality control to meet the demands of automotive, industrial, and consumer electronics applications.
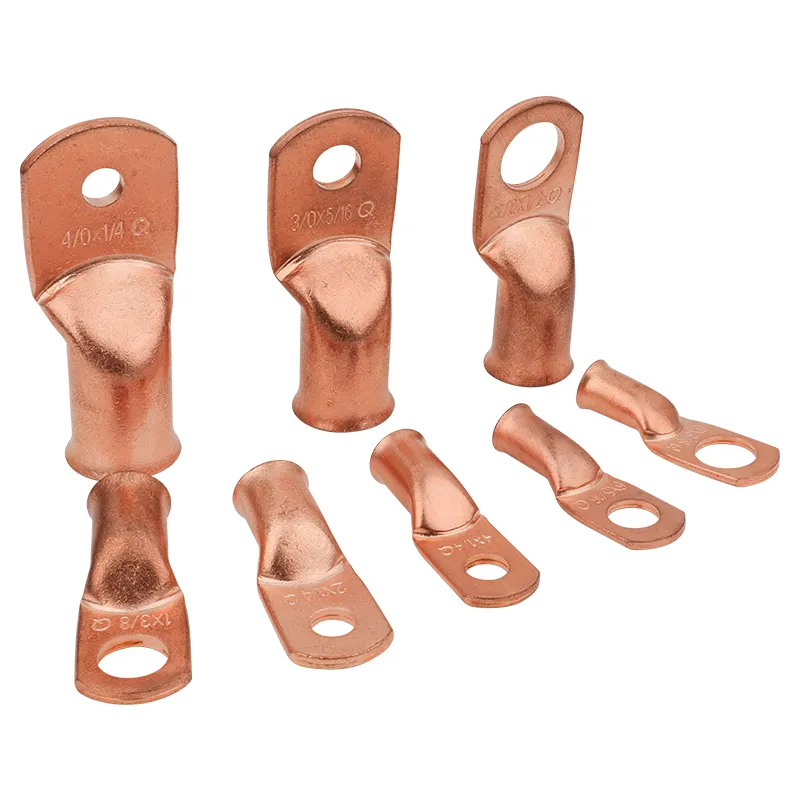
Features:
Attribute | Details |
Character | Insulation |
Species | Terminal |
Production Process | Welding |
Shape | Custom |
Interface Type | Custom |
Brand | OEM |
Tolerance | +/- 0.01mm |
Shipment Terms | Express / Air Freight / Sea Freight |
Quality Control | 100% Inspection Before Shipping |
Service | OEM |
Dimensions | As per Drawings or Samples |
Certificates | ISO9001:2015, IATF16949, RoHS, REACH |
Drawing Format | PDF, 2D/3D/DWG/IGS/STEP/Solidworks |
Packaging | OPP Bag, Custom |
Place of Origin | Xiamen, China |
Production Capacity | 10,000 units |
Production Process:
- Material Inspection: The raw materials, such as copper, brass, or aluminum, are carefully inspected for quality and consistency. Equipment like material testing machines and spectrometers are used to verify the metal’s conductivity and purity.
- Stamping/Forming: The initial shape of the connectors is formed through stamping or die-casting. Precision stamping machines and die-casting equipment are employed to ensure the connectors are produced to exact specifications.
- Welding: For connectors that require multiple parts, the welding process ensures a strong, reliable bond. High-frequency welding machines or laser welders are utilized for precision and strength.
- Machining: Post-forming, connectors undergo precision machining for final shaping and hole drilling. CNC machines, such as vertical and horizontal milling machines, ensure tight tolerances, down to +/- 0.01mm.
- Surface Treatment: To enhance corrosion resistance, connectors are coated with materials such as tin or nickel. Electroplating machines and coating systems ensure uniform coverage and high-quality finishes.
- Quality Control & Testing: Each connector undergoes rigorous inspection, including dimensional checks, conductivity tests, and mechanical performance assessments. Equipment like coordinate measuring machines (CMM) and conductivity testers are used to verify the final product’s quality.
- Final Inspection and Packaging: The final products are visually inspected for defects, and a 100% inspection process is carried out before packaging. Automated inspection systems and manual checks ensure no defects are shipped. The connectors are then carefully packaged in custom boxes or OPP bags to protect them during transit.
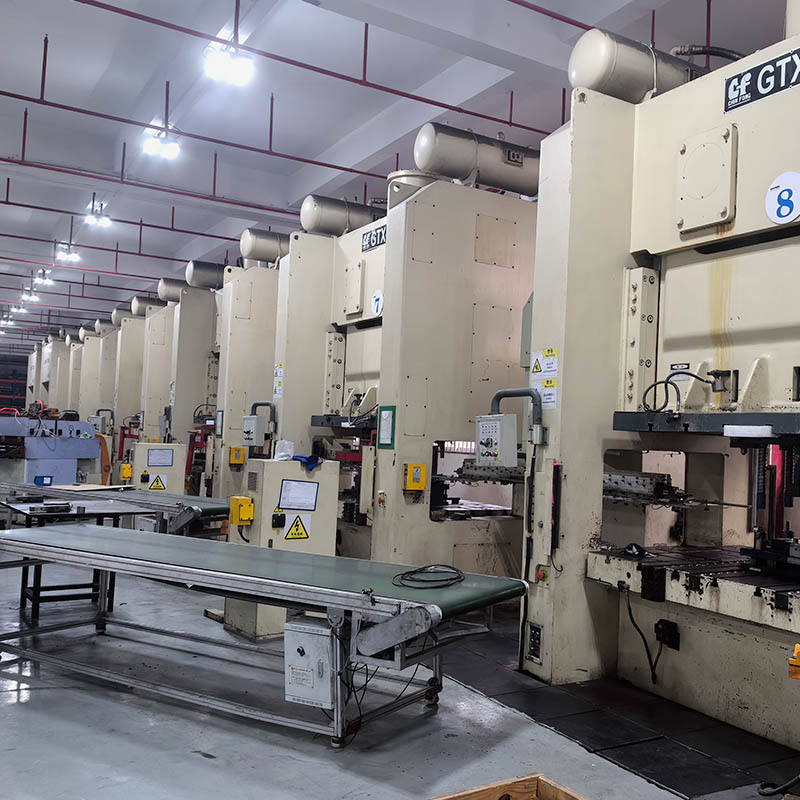
Surface Treatments:
- Tin Plating: A common surface treatment, tin plating provides excellent corrosion resistance and improved solderability. This is ideal for connectors exposed to harsh environmental conditions.
- Nickel Plating: Nickel plating offers enhanced durability and resistance to corrosion, making it suitable for applications where high mechanical strength and resistance to wear are required.
- Gold Plating: Gold plating is used for applications requiring excellent electrical conductivity and resistance to oxidation, particularly in high-performance or sensitive electronic systems.
- Silver Plating: Silver plating is applied for its superior electrical conductivity, commonly used in high-current applications. It also offers moderate corrosion resistance, ideal for use in environments with low to medium exposure to corrosive elements.
- Phosphate Coating: A phosphate coating helps improve corrosion resistance and provides a lubricating surface, ideal for connectors that require enhanced durability under mechanical stress.
- Electroless Plating: This method provides uniform coating thickness without the need for electrical current. It is used for applications requiring precise coating on intricate shapes and offers excellent wear resistance.
Why Choose Us?
– Experienced OEM and Assembly Services: Offering tailored OEM solutions and assembly services since 2000, we provide comprehensive support for your manufacturing needs.
– One-Stop Sourcing Solution: We specialize in a wide range of components, including stamping parts, CNC lathe and milling parts, springs, shafts, fasteners, and more, streamlining your procurement process.
– Product Certifications: Our products meet global standards, with certifications including RoHS and IATF16949, ensuring quality and compliance.
– Industry-Leading Management Certifications: We are ISO 9001:2015 and IATF16949 certified, demonstrating our commitment to high-quality management systems and continuous improvement in every aspect of our operations.