When planning a project that involves custom silicone products, cost is a crucial element that influences your production strategy and final product pricing. Several interconnected factors drive the overall cost of manufacturing, and understanding these variables can help you streamline your process, make informed decisions, and ultimately optimize your budget. In this blog, we will explore the primary elements that affect the cost of custom silicone products and offer insights on how you can navigate these factors to achieve cost-effective manufacturing without compromising on quality.
-
Mold Complexity
The complexity of the mold used in the production of silicone products is one of the most influential factors affecting cost. Molds can range from simple single-cavity designs to intricate multi-cavity molds designed for high-volume production. Generally, the more complex the mold design, the higher the associated costs.
Single-Cavity Molds are relatively straightforward and ideal for low-volume production runs. These molds are less expensive upfront but are not as efficient for mass production due to the higher per-unit cost.
Multi-Cavity Molds, on the other hand, enable the production of several parts in a single cycle, leading to reduced per-unit costs when manufacturing in large quantities. Although they come with a higher initial cost, the increased efficiency they provide in large-scale production helps offset the initial investment. For manufacturers focused on long-term production runs, multi-cavity molds are often the more economical choice.
-
Silicone Material Selection
The choice of silicone material is another significant determinant in the overall cost. Silicone products are made from various types of silicone compounds, each offering unique properties suited to specific applications. The material type impacts both the cost of the raw material and the processing methods required.
– Liquid Silicone Rubber (LSR): LSR is a highly fluid silicone material often used for complex, high-precision designs, making it ideal for industries like medical, automotive, and electronics. The processing of LSR requires specialized equipment, and its higher price is reflective of the complex molding process involved. However, its superior durability and flexibility make it the material of choice for products that need to withstand extreme conditions or meet stringent regulatory standards.
– High Consistency Rubber (HCR): HCR is a more rigid silicone material commonly used for larger, simpler parts. It is less expensive compared to LSR, as it can be molded using standard compression molding processes that are less intricate and less costly. HCR is ideal for industrial applications where high-performance characteristics and precision are not as critical.
Choosing between these materials depends on the specific requirements of your application, balancing both performance and cost considerations.
-
Production Volume
The volume of units you plan to produce plays a vital role in determining the per-unit cost. Custom silicone products benefit greatly from economies of scale. As production quantities increase, the fixed costs—such as mold design, setup, and tooling—are distributed over a larger number of parts, lowering the cost per unit.
Low-Volume Production: For smaller orders or prototype runs, the cost per unit tends to be higher due to the smaller number of units produced. This is because a significant portion of the setup costs is amortized over a smaller batch, making smaller production runs less cost-effective.
High-Volume Production: Large-scale production runs take advantage of economies of scale, reducing the per-unit cost. The higher the volume, the more cost-effective the production process becomes, and this ultimately makes mass production a more affordable option for many businesses.
-
Manufacturing Process
The method used to produce your silicone products can significantly impact both the initial investment and the final cost per unit. The most common silicone manufacturing processes include injection molding, compression molding, and LSR molding. Each of these processes offers distinct advantages and is suited to different production needs.
– Injection Molding: This is a high-precision, high-volume manufacturing process ideal for producing intricate parts with complex geometries. It uses high-pressure liquid silicone rubber (LSR) injected into custom molds, making it perfect for high-precision applications. While the initial cost of equipment and tooling can be high, injection molding is extremely cost-efficient for large production runs.
– Compression Molding: This process involves placing pre-measured silicone material into an open mold, which is then closed and heated. Compression molding is generally less expensive than injection molding, making it a good option for medium to high-volume production. However, it is not suitable for highly intricate designs, as it lacks the precision of injection molding.
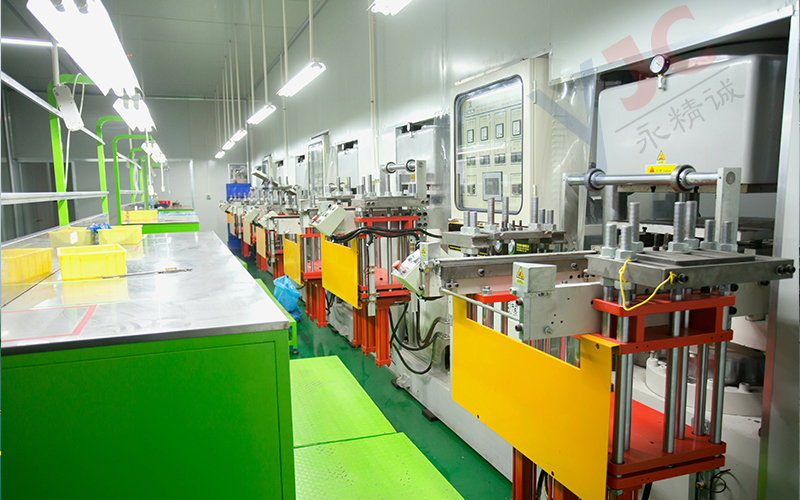
– Liquid Silicone Rubber (LSR) Molding: LSR molding is typically used for medical-grade, food-grade, and high-performance applications. This process requires specialized equipment and often takes place in cleanroom environments. While LSR molding may involve a higher initial investment, it ensures precision and meets stringent industry standards, making it ideal for products that demand exceptional reliability and safety.
-
Quality and Certification Requirements
For custom silicone products, especially those used in regulated industries such as healthcare and food, meeting industry certifications and quality standards is essential. Certifications like ISO 13485 (for medical devices), FDA approval (for food-grade products), and RoHS compliance (for electronics) are necessary to demonstrate that products meet both regulatory and safety standards.
Achieving these certifications requires additional testing, validation, and documentation, which inevitably adds to the overall cost. However, obtaining these certifications ensures that your products are compliant with global industry standards, giving customers confidence in the quality and safety of the product.
-
Prototyping and Design Costs
Before full-scale production can begin, a significant amount of time and resources are often invested in prototyping and design modifications. Prototyping allows manufacturers to test and refine the design, making sure it meets functional and aesthetic requirements. This stage often involves several iterations, which can raise costs, especially if the product design is complex.
Incorporating customer feedback during the prototyping phase may also necessitate additional design cycles, further increasing the upfront costs. However, investing in thorough prototyping can save money in the long term by preventing costly mistakes during full-scale production.
-
Additional Costs for Testing and Quality Control
To ensure that custom silicone products meet the necessary performance and safety standards, manufacturers often conduct extensive testing. This can include testing for mechanical properties, chemical stability, durability, and environmental resistance. While these tests are vital for ensuring product reliability, they also contribute to the overall cost of manufacturing.
For products in regulated industries, additional testing may be required to meet industry standards, adding further costs to the production process. However, these expenses are necessary for maintaining the high quality and safety of the final product.
Conclusion
Understanding the key factors that affect the cost of custom silicone products is essential for optimizing your manufacturing process and controlling expenses. By carefully considering mold complexity, material selection, production volume, and manufacturing processes, you can make strategic decisions that balance cost and quality effectively.
At YJCPolymer, we specialize in providing cost-effective silicone solutions without compromising on product performance, durability, or safety. Our team is dedicated to guiding you through the design, prototyping, and production phases to ensure that your custom silicone products meet your specifications while remaining within your budget.
If you are ready to get started with your custom silicone product or need a tailored quote for your project, feel free to contact us today. Our experts are here to help you navigate the process and ensure you get the best value for your investment.