Overview:
Custom plastics injection molding tooling for home appliances involves the design and manufacture of specialized molds used to produce plastic components for various household devices. This process primarily utilizes advanced techniques such as precision injection molding, where molten plastic is injected into custom-designed molds to create intricate shapes and features. The production typically requires high-performance machinery, including injection molding machines, CNC machining centers, and EDM (Electrical Discharge Machining) equipment, ensuring high accuracy and efficiency. Our factory offers OEM services for tooling, allowing us to create tailored solutions that meet specific client requirements. Additionally, we provide a range of surface finishing options to enhance both the functionality and appearance of the final products, reflecting the unique characteristics and demands of home appliance manufacturing.
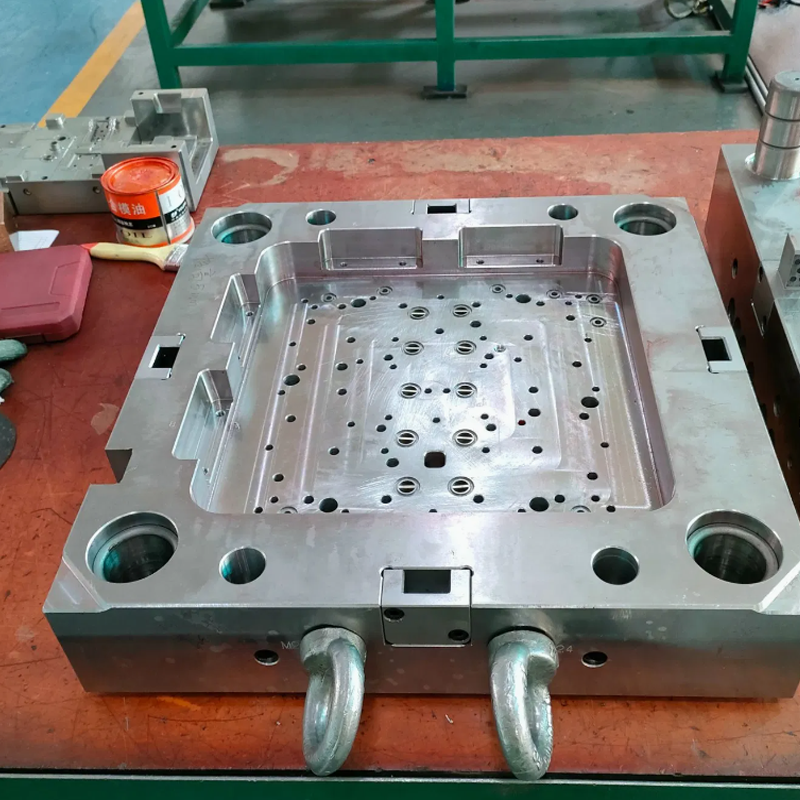
Specifications:
Category | Details |
Mold Type | Plastic Injection Mold |
Mold Material Options | P20, 718, 738, NAK80, S136 |
Mold Base Standards | HASCO, DME, MISUMI, JIS, LKM |
Mold Runner System | Cold Runner / Hot Runner |
Mold Gate Options | Slide Gate, Sub Gate, Pin-point Gate |
Cavity | Single or Multi-Cavity |
Design Software Supported | UG, PROE, CAD, SOLIDWORKS |
Molding Equipment Used | CNC, Wire Cutting, Milling Machine, EDM |
Compatible Raw Materials | ABS, PP, PC, PA6, PA66, PVC, POM, PMMA, PS |
Packaging Method | Wooden pallet or carton |
OEM Services | Available—please provide 2D/3D files or samples |
Lead Time | Approximately 30 days |
Production Process:
- Initial Consultation: We begin by gathering samples, drawings, and specific requirements from you to ensure a clear understanding of your needs.
- Mold Design: After you place your order, we collaborate closely with you to refine the mold design, exchanging ideas and feedback to optimize functionality.
- Material Procurement: We source high-quality materials, including steel and mold base components, necessary for the tooling process.
- Assembly: Our skilled team assembles the mold components, ensuring precise fit and alignment.
- Mold Inspection: Throughout the tooling process, we conduct thorough inspections to maintain quality control and adherence to specifications.
- Mold Testing: We will notify you of the testing date, after which we will send samples for your review and approval.
- Shipping Confirmation: Upon your instruction and confirmation, we prepare the molds for shipment.
- Final Preparation: The completed molds are meticulously checked and readied for packing.
- Comprehensive Services: We offer a wide range of mold services, including plastic injection molds, blow molds, silicone molds, and die casting molds, tailored to meet diverse production needs.
Surface Treatment Options:
- Polishing: A process that enhances surface smoothness and shine, providing a high-quality finish that reduces friction and improves aesthetics.
- Matte Finish: This treatment results in a non-reflective surface, offering a sleek, modern look while minimizing visibility of fingerprints and scratches.
- VDI (Verein Deutscher Ingenieure): A standardized surface finish method that specifies surface texture and roughness, ensuring consistency and precision in molded parts.
- SPI (Society of the Plastics Industry): This treatment adheres to industry standards for surface finishes, categorizing the texture of the mold surface to meet specific application requirements.
- Ball Burnishing: A mechanical finishing process that employs ball-shaped tools to smooth and polish surfaces, enhancing surface hardness and improving overall durability.
Our Advantages:
- Confidentiality: We prioritize the protection of your sensitive information by utilizing signed Non-Disclosure Agreements (NDAs). Our staff undergoes training on confidentiality protocols, ensuring that sensitive data is only shared on a need-to-know basis.
- Proactive Communication: With years of successful collaboration with our partners, we are committed to delivering high-quality results at competitive prices. Our dedicated team is not only focused on quality and on-time delivery but is also proactive in addressing any issues that may arise during the process.
- Responsive Service: For urgent matters, we offer 24/7 support to provide timely feedback. Our team is committed to responding to emails within 12 hours or sooner, leveraging smartphone technology to ensure quick communication. We encourage you to connect with us via WhatsApp or WeChat for enhanced interaction.
- Cost Advantages: We are eager to assist with your other projects requiring outsourcing services. Our aim is to help reduce your plant visit and transportation costs. Our team’s mission is to identify the best pricing options while maintaining high-quality standards, fostering trust and confidence on both sides.
Our Factory:
YJC operates from a spacious 4,500㎡ facility and brings over 20 years of expertise in OEM services. Our factory is outfitted with state-of-the-art processing machinery, including Roders, Makino, Sodick, and YCM, which allows us to achieve micron-level precision in tooling manufacturing. Leveraging advanced equipment such as ARBURG, Miltitech, and 2KM, we are capable of producing ultra-precision components with weights as light as 0.02g and thicknesses as thin as 0.1mm. Furthermore, our ISO-certified Class 8 medical dust-free workshop provides a controlled manufacturing environment for medical device components, ensuring adherence to the highest standards of cleanliness and precision.
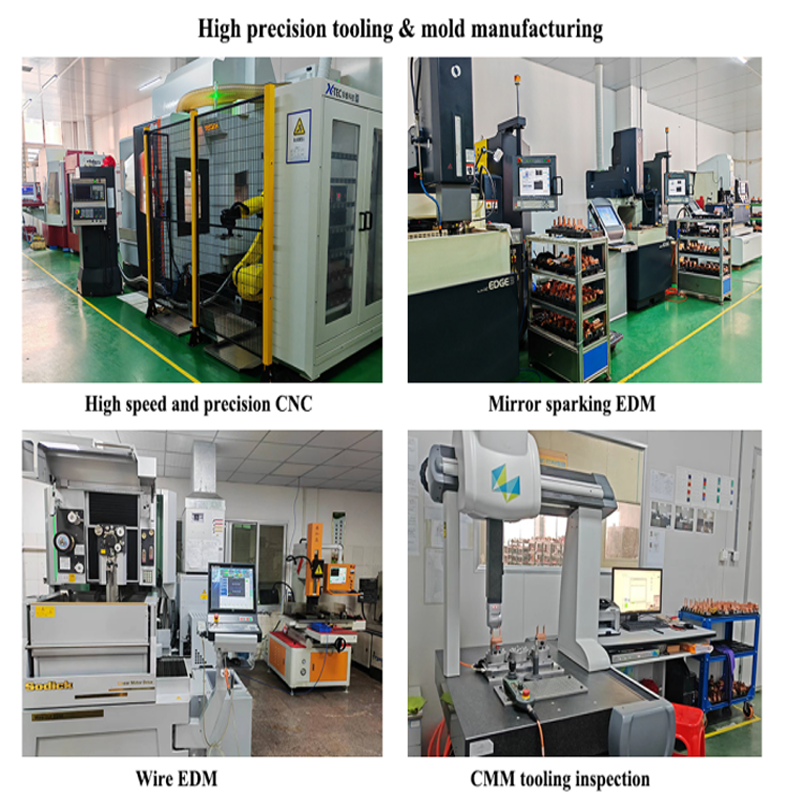