Overview:
The Lead Frame for the Ford F-150 is an essential component in the vehicle’s electronic systems, designed to provide reliable electrical connections and mechanical support. This component is typically manufactured using advanced metal stamping and etching processes, ensuring precision and consistency. It is primarily made from high-conductivity materials such as copper alloys or specialized steel to guarantee optimal performance and durability. Our state-of-the-art equipment and cutting-edge technology enable us to offer customization options for various sizes and specifications, tailored to meet your specific requirements. With our expertise and advanced manufacturing capabilities, we ensure a perfect fit and superior quality for your application.
Details:
- Purpose: Replace/Repair
- Place of Origin: Xiamen, China
- Size: Standard
- Type: TCU
- Brand Name: OEM
- Car Model: Ford F-150, Navigator, Expedition
- MOQ: According to your design
- Quality: High-Quality, total tested
- Shipping: DHL, UPS, EMS, FEDEX, TNT
- Delivery time: About 10-15 days
- Sample: Available
- Material: Copper alloys
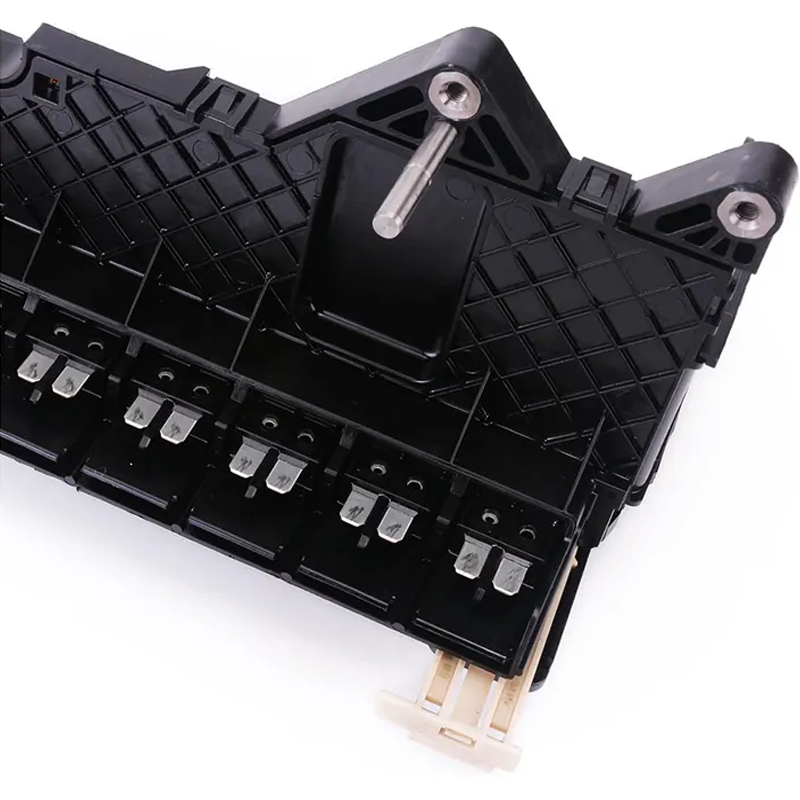
Surface Treatment:
Nickel Plating:
Nickel plating is a process that involves coating the lead frame with a thin layer of nickel. This treatment enhances the corrosion resistance, wear resistance, and overall durability of the lead frame. It also provides a smooth and conductive surface, which is essential for reliable electrical connections in electronic components.
Galvanization:
Galvanization involves applying a protective zinc coating to the lead frame to prevent rust and corrosion. This process is particularly beneficial for lead frames used in harsh environments, as it significantly extends the lifespan of the component by providing robust protection against environmental factors.
Powder Coating:
Powder coating is a dry finishing process where a powder material is applied electrostatically to the lead frame and then cured under heat. This results in a high-quality, durable finish that is resistant to chipping, scratching, and fading. Powder coating also offers excellent electrical insulation properties, making it ideal for electronic applications.
Anodizing:
Anodizing is an electrochemical process that converts the metal surface into a durable, corrosion-resistant, anodic oxide finish. This treatment is commonly used for aluminum lead frames and enhances their surface hardness, wear resistance, and aesthetic appearance. Anodized surfaces can also be dyed in various colors, providing additional customization options.
Production Process:
- Material Selection
High-quality copper alloys or stainless steel are chosen for their conductivity and strength, ensuring the lead frame can handle the electrical and thermal demands of automotive applications.
- Stamping
Progressive die stamping precisely forms, cuts, and punches the metal into the required intricate design, maintaining tight tolerances for consistent production quality.
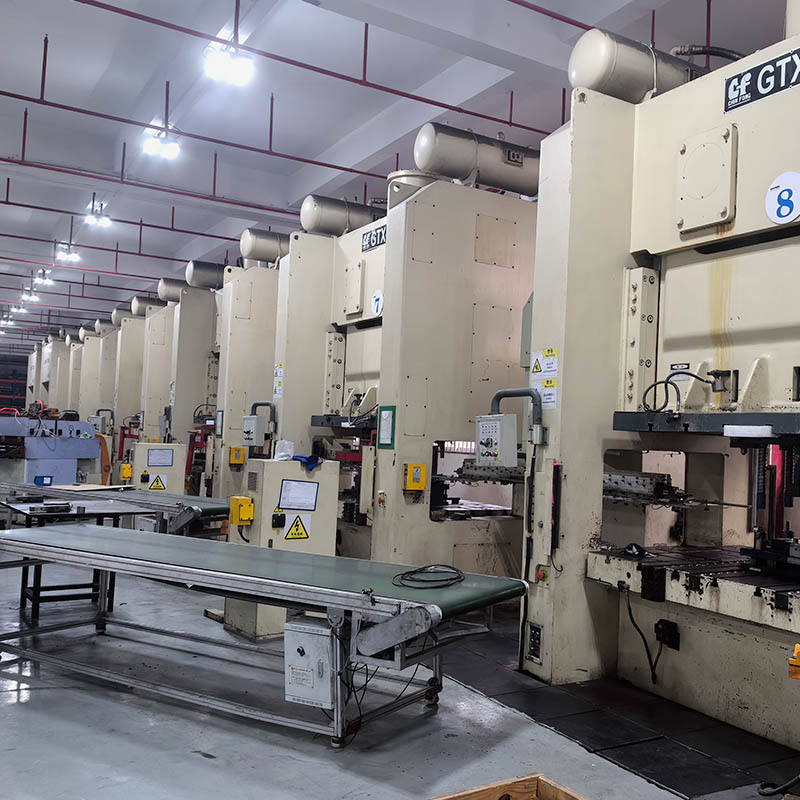
- Plating
The lead frame is electroplated with conductive materials like nickel, gold, or silver, enhancing corrosion resistance, electrical performance, and solderability.
- Etching and Cleaning
Chemical etching refines the dimensions and cleans the surface, ensuring smooth edges and reliable electrical contact points.
- Annealing
If necessary, annealing is performed to improve ductility and reduce internal stresses, preventing brittleness during further processing.
- Inspection and Testing
Each lead frame undergoes detailed inspection and testing to ensure it meets all dimensional and electrical standards.
- Packaging and Shipping
The final lead frames are carefully packaged and shipped to assembly plants, ready for integration into the Ford F-150’s electrical systems.
Factory Show:
We operate advanced, fully automated production lines, supported by a highly skilled and certified quality control team. Our facility is equipped with state-of-the-art machinery, including automatic drying lines, high-speed automatic screen printing machines, 3D measuring instruments, precision CNC machines, automatic high-speed doming machines, die-cutting machines, and automated die-cutting systems, among others. These cutting-edge tools enable us to deliver exceptional precision, efficiency, and quality across all production processes.
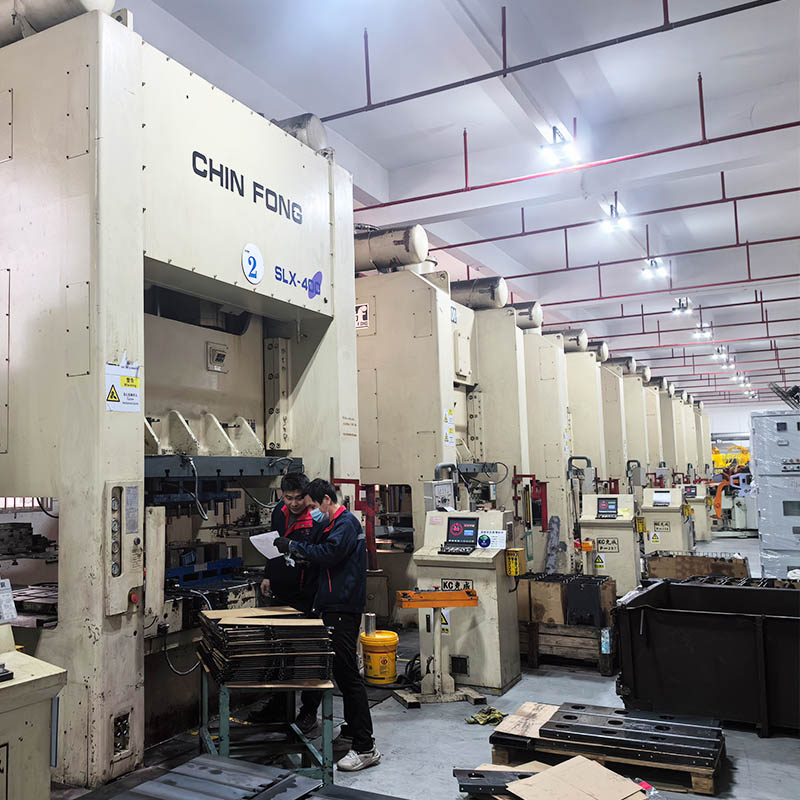
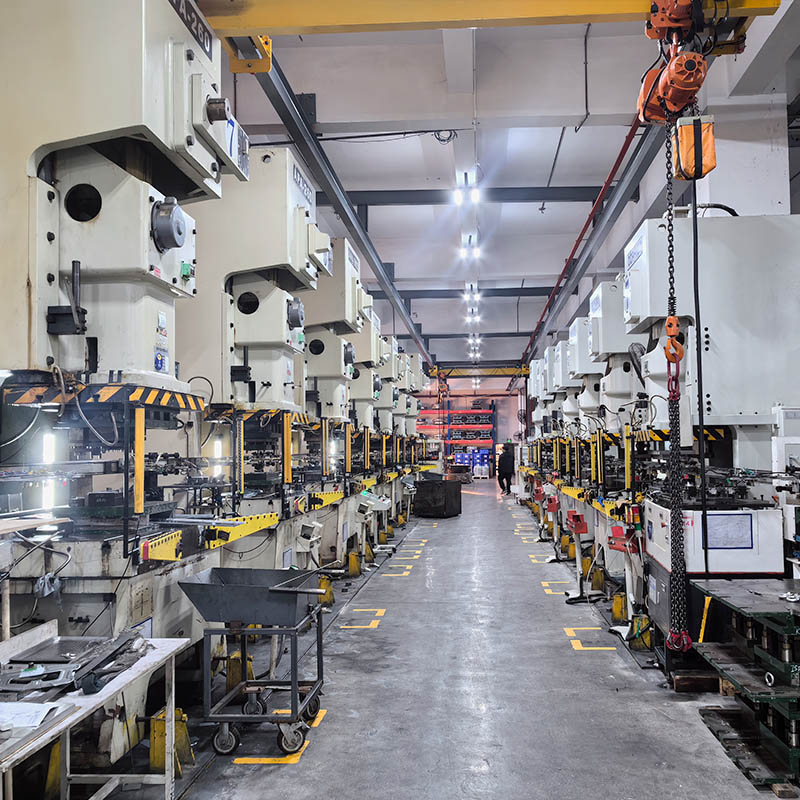