Overview:
Copper busbars for automotive parts are essential components used for electrical power distribution and grounding in vehicles, typically made from high-conductivity copper or copper alloys. These busbars are manufactured through advanced metal stamping and precision machining processes to ensure optimal electrical performance and durability. Our factory offers a one-stop service, providing custom solutions with a variety of material options such as pure copper, copper alloys, and other conductive metals. We also offer multiple surface treatments, including tin plating, nickel plating, and powder coating, to enhance corrosion resistance and conductivity. Equipped with cutting-edge machinery, including CNC machines and automated stamping lines, we ensure high-quality production tailored to your specific requirements.
Features:
Category | Details |
Surface Processing | Electroplating, Fine Blanking, Multi-Position Process, Forming Process |
Industry | Metal Stamping Parts |
Tolerances | 0.02mm |
Certificate | RoHS / ISO9001:2015,IATF16949 |
Material Available | Copper, Stainless Steel, Carbon Steel, Aluminum, etc. |
Usage | Automotive, Agriculture, Furniture, Machinery |
Press Capabilities | 16 ton – 300 ton |
Stamping Capacity | Deep Drawing, Shaping Metal |
Stamping Die | In-House Die Making |
Samples | Free Available |
Service | OEM |
File Format | CAD, SolidWorks, PDF, etc. |
Transport Package | As Per Your Requests |
Trademark | OEM |
Origin | Xiamen, China |
Working Process:
- R&D and Engineering
The process begins with research and development, where our engineering team works closely with clients to understand their specific requirements and performance expectations for copper busbars. Using advanced design software, our engineers create detailed plans and simulations to optimize functionality and durability while ensuring compliance with industry standards.
- Tooling
Once the design is finalized, precision tooling is developed in-house. This stage involves creating custom molds and dies that are necessary for shaping the copper busbars according to the specifications. Our tooling department uses state-of-the-art CNC machines to ensure high accuracy and repeatability.
- Sample Approval
Before mass production begins, prototype samples are created and submitted for customer approval. This stage is critical for validating the design and ensuring that the product meets all technical and aesthetic requirements. Any necessary adjustments are made at this point to fine-tune the final product.
- Mass Production
After receiving sample approval, mass production commences using high-precision stamping and forming processes. Our automated production lines ensure efficient, large-scale manufacturing while maintaining consistency in quality. Throughout production, we employ techniques like deep drawing and shaping to create copper busbars that meet tight tolerances and complex geometries.
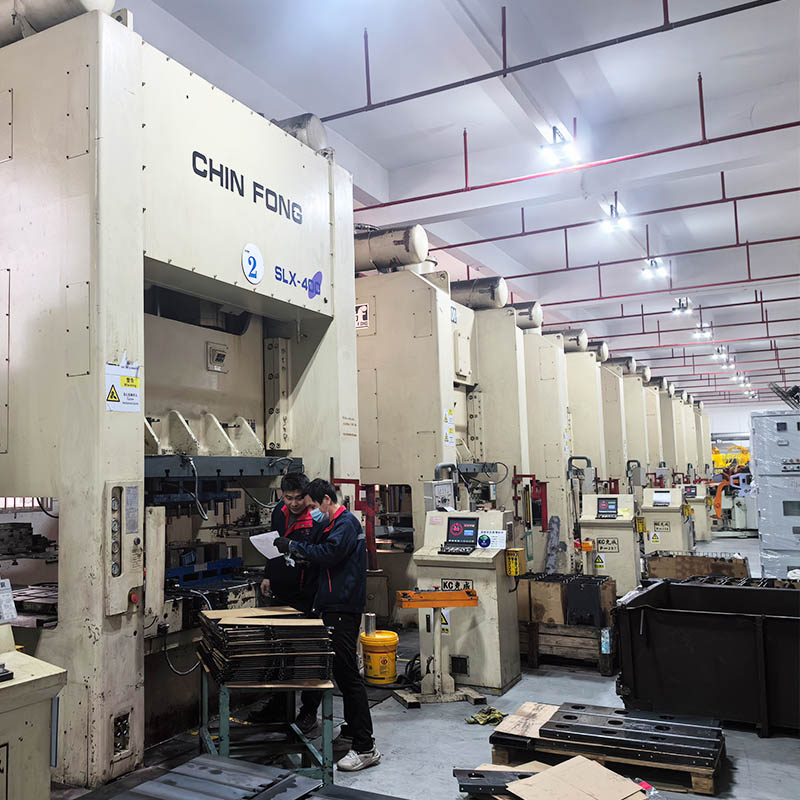
- QC Inspection
Quality control is integrated throughout every phase of production. Our dedicated QC team conducts rigorous inspections, including dimensional checks and material analysis, to ensure that each busbar meets the highest standards. These inspections follow strict protocols, such as ISO 9001:2015, to ensure product reliability and performance.
- Packing
The final step in the process is secure packing and shipment. Each batch is carefully packaged to protect the busbars from damage during transportation. Customized packaging solutions are available based on client requests, ensuring that products arrive safely and ready for use.
Surface Treatment Options:
- Plating:
A process that coats metal surfaces with a thin layer of zinc, nickel, or chrome to improve corrosion resistance and conductivity.
- Powder Coating:
An electrostatic application of powder followed by heat curing, creating a durable, wear-resistant finish.

- Anodizing:
An electrochemical process for aluminum, forming a protective oxide layer to enhance hardness and corrosion resistance.
- Painting:
Application of liquid paint for protective and decorative finishes, offering flexibility in color and texture.
- Electrophoresis (E-coating):
A water-based coating process using electric current for even, corrosion-resistant coverage.
- Polishing:
A mechanical process that smooths and shines surfaces, improving appearance and reducing friction.
Why Choose Us?
- In-House Manufacturing:
Our factory enables stringent quality control, ensuring that our products meet the highest standards while maintaining competitive pricing.
- Extensive Industry Experience:
With nearly 20 years of expertise in manufacturing metal stamping parts, we have developed a deep understanding of industry requirements and best practices.
- Advanced Quality Assurance:
Equipped with state-of-the-art testing equipment and a dedicated quality control team, we ensure the reliability and consistency of our products.
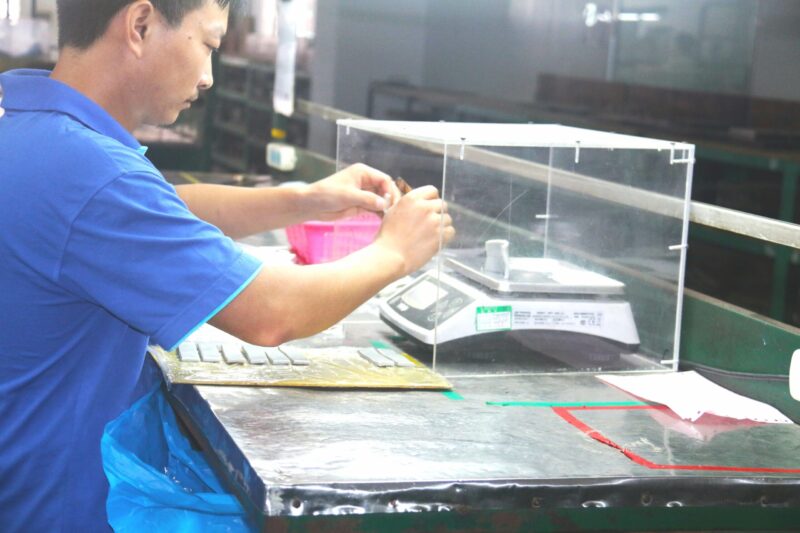
- Research and Development:
Our experienced technicians in the R&D department work closely with clients to provide tailored OEM services, ensuring that we meet your specific needs effectively.