Overview:
Plastic LSR (Liquid Silicone Rubber) overmolding cup accessories are engineered for enhanced durability, flexibility, and wear resistance. Manufactured through the LSR overmolding process, liquid silicone rubber is molded around a plastic core, creating a robust, multi-material product that combines the strength of plastic with the resilience of silicone.
Our factory offers Custom and OEM services for LSR overmolded cup accessories, with customizable sizes, colors, and specific applications. As a reliable supplier and manufacturer, we ensure precise, high-quality production tailored to your needs.
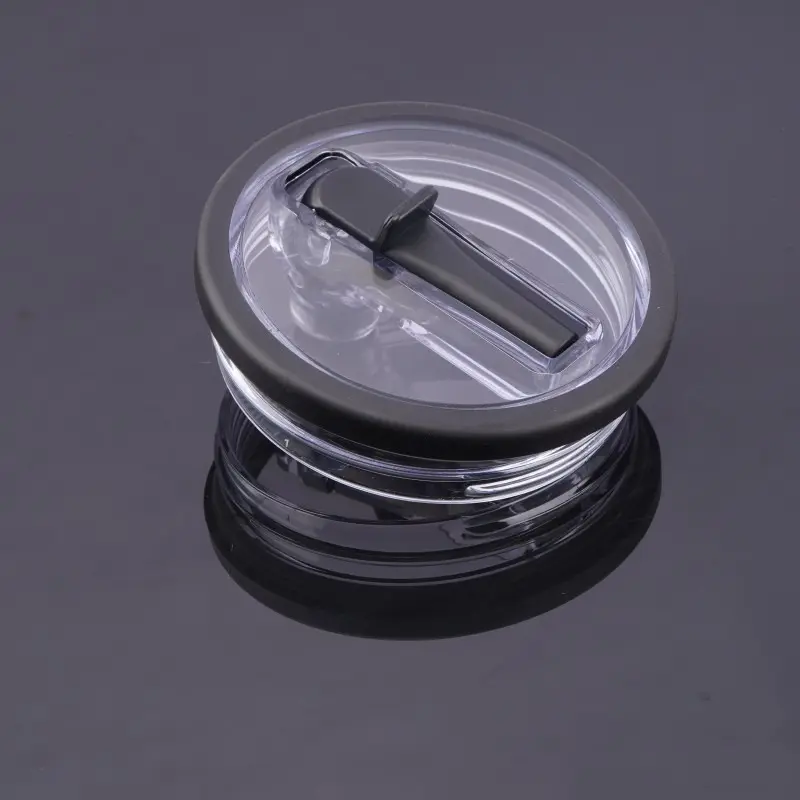
Characteristics:
Attribute | Details |
Place of Origin | Xiamen, China |
Brand Name | OEM |
Material | Plastic, LSR |
Function | Leakage-proof |
Features | 100% Leakage-proof |
Logo | Accept Customized Logo |
Package | Custom Package |
Size | Custom |
Color | Multi-color |
Delivery Time | 7-15 Working Days |
Sample | Available |
Certifications | ISO9001, IATF16949 |
Production Process:
- Mold Design and Preparation: First, the mold is designed to accommodate both the plastic core and the silicone overmolding. It is carefully prepared to ensure precision in the final product.
- Plastic Injection Molding: The first step in the overmolding process involves injecting the plastic material into the mold to form the core of the cup lid accessory. This step shapes the rigid base that will support the silicone layer.
- LSR Injection: After the plastic core is formed, Liquid Silicone Rubber (LSR) is injected around the plastic part in a second molding stage. The LSR is heated and cured in the mold, bonding tightly to the plastic surface to create a durable, flexible overmold.
- Curing: The silicone is then cured under heat to ensure it sets properly and forms a strong bond with the plastic core, enhancing the product’s strength and performance.
- Cooling and Ejection: Once the overmolding process is complete, the molded cup lid accessory is cooled to solidify the silicone, and then ejected from the mold.
- Quality Control and Inspection: The final product undergoes a thorough quality inspection to ensure it meets the required specifications for functionality, such as being leakage-proof, and checks for any defects.
- Packaging: After passing quality control, the cup lid accessories are packaged according to customer requirements, ready for shipment.
Why Choose Us?
- Commitment to Quality and Integrity: We prioritize the highest standards of quality and uphold a strong commitment to integrity in every aspect of our business.
- Certifications: Our processes are certified with ISO9001and IATF16949, ensuring consistent quality management and manufacturing excellence.
- Robust Supply Capacity: We maintain adequate supply capacity to meet both large-scale and custom orders efficiently.
- On-Time Delivery: Our streamlined production process ensures punctual delivery, meeting your project timelines.
- Comprehensive OEM and One-Stop Services: We offer OEMsolutions and a complete range of one-stop services, providing seamless support from design to final product delivery.
Factory Show:
We operate a fully equipped facility featuring advanced mold-making technology, including CNC machines, Mirror EDM, EDM, and Slow-speed Wire Cut WC. Our production capabilities extend to 15 rubber compression machines and 2 LSR injection machines, with a focus on overmolding expertise. To uphold stringent quality standards, we employ 3D projectors, sealing testers, elasticity measurement tools, durometers, and a dedicated QC team. Our mechanical equipment also includes AutoDryer Lines, automatic screen printing machines, 3D measuring instruments, high-speed doming machines, and CNC machines, all working together to ensure the highest quality production across all stages.