Overview:
The Silicone Ice Ball Tray Mold for Homemade Juice is a durable, food-grade silicone mold designed to create perfectly shaped ice balls for beverages like whiskey, cocktails, and fresh juices. Manufactured using advanced silicone injection molding techniques, it offers flexibility and easy ice removal. At YJCPolymer, we offer OEM and custom services to create tailored ice ball trays for various applications, ensuring optimal performance and aesthetic appeal for both personal and commercial use.
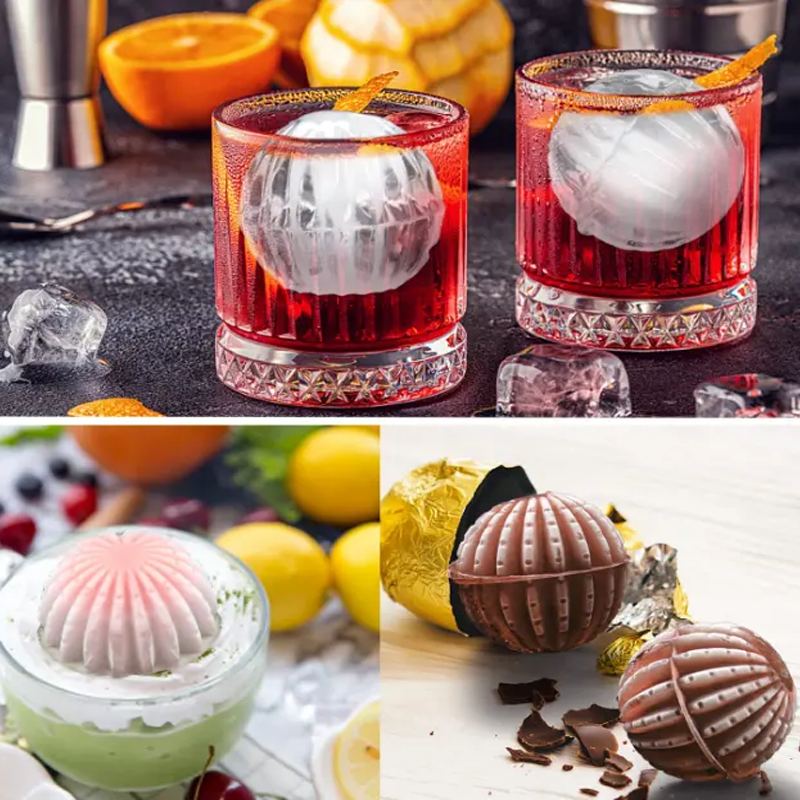
Features:
Attribute | Details |
Place of Origin | Fujian, China |
Brand Name | OEM |
Material | Silicone |
Size | Custom |
Packaging | OPP bag or customized packaging |
Color | Custom |
Logo | Custom |
Feature | Easy pop-out |
Certification | Necessary standards available |
Product Advantages:
- Constructed from eco-friendly silicone, this product is designed for long-lasting use, with exceptional heat and cold resistance, maintaining performance within a temperature range of -60°C to +200°C.
- Available in vibrant colors and a variety of shapes to suit different preferences.
- Effortlessly cleanable and reusable, providing added convenience.
- Retains its color and appearance over time, ensuring long-term durability without fading.
Production Process:
- Material Selection
High-quality, food-grade silicone is carefully selected for its durability, flexibility, and resistance to temperature variations. This ensures that the mold is safe for food use and performs well in extreme temperatures.
- Mold Design and Prototyping
The mold design is developed to meet specific product requirements, with a focus on ease of use, functionality, and aesthetic appeal. A prototype is created to test the design’s efficiency before full-scale production begins.
- Silicone Molding
The silicone material is injected or poured into pre-designed molds, where it is then cured to harden and set into the desired shape, such as round ice balls. This process ensures a precise fit and smooth texture.
- Cooling and Curing
The mold is cooled to ensure the silicone sets properly. This stage guarantees the final product’s flexibility and strength, essential for long-term durability and ease of use.
- Quality Control
The finished molds undergo rigorous quality checks to ensure that each tray meets strict standards for size, shape, and material integrity. Any defective products are removed from the production line.
- Cleaning and Packaging
After quality inspection, the molds are cleaned to remove any residual material. The final product is then packaged in custom packaging, ready for shipping or distribution.
Factory Show:
Our facility is equipped with advanced machinery to ensure superior production quality. We utilize cutting-edge equipment, including CNC machines, Mirror EDM, Slow-speed Wire Cut WC, and specialized auxiliary tools for precise mold-making. Our production lines feature 15 rubber compression machines and 2 LSR injection molding machines, complemented by 3D projectors, sealing testers, and durometers for rigorous quality control.
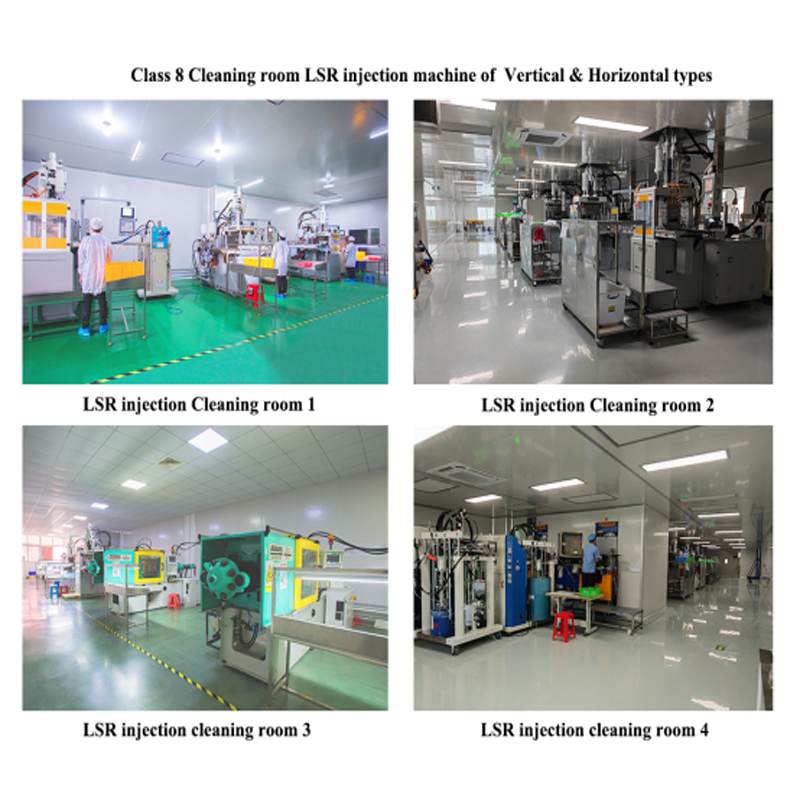
Additionally, our automated systems include an AutoDryer Line, screen printing machines, 3D measuring instruments, and high-speed doming machines. As an ISO9001 and IATF16949 certified manufacturer, we uphold the highest quality standards through automated processes, advanced machinery, and stringent quality oversight.