Overview:
Premium Whisky Silicone Ice Cube Tray, expertly crafted from high-quality food-grade silicone using advanced Liquid Silicone Rubber (LSR) injection molding technology. Designed to enhance the whisky tasting experience, it minimizes dilution with precisely molded, slow-melting ice cubes that preserve the spirit’s flavor profile. We offer both OEM and custom design services to accommodate specific size, shape, and branding requirements, ensuring a tailored solution for your unique needs.
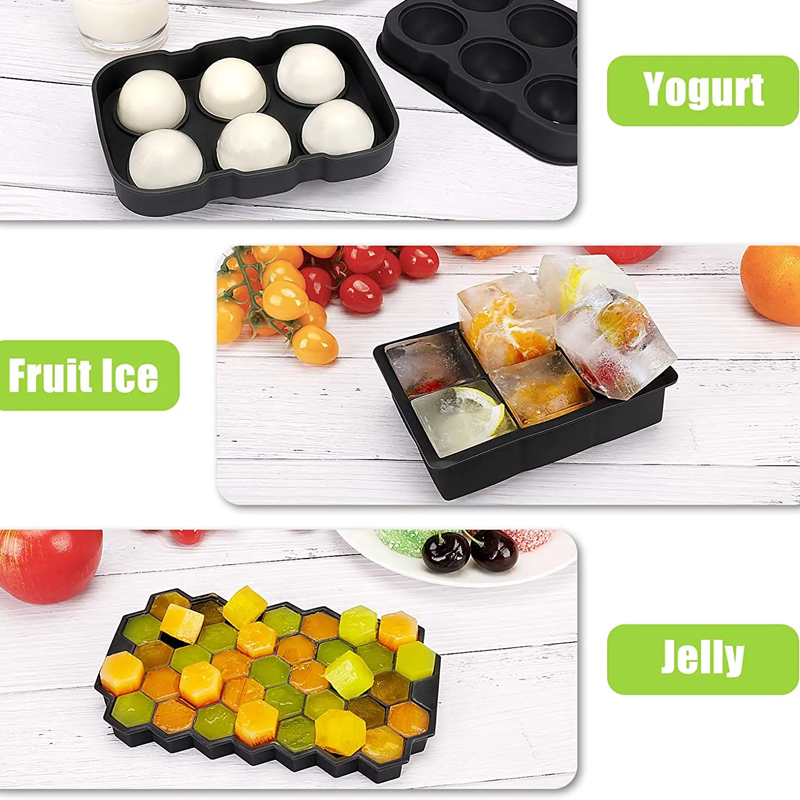
Details:
Specification | Details |
Place of Origin | Xiamen, China |
Brand Name | Eco-life |
Usage | Making Ice Cubes |
Color | Black or Any Pantone Color |
Size | Custom |
Logo | Customized Logo Acceptable |
OEM | Acceptable |
MOQ | According to your requirement |
Packing | Custom |
Sample | Available |
Advantages of Our Silicone Ice Cube Tray:
- Made from Soft, Food-Grade Silicone
- BPA-Free and Safety Tested
- Dishwasher, Freezer, Oven, and Microwave Safe
- Eco-Friendly and Non-Toxic
- Soft, Flexible Design
- Temperature Resistant from -40°C to +230°C
Production Process:
- Design and Customization
The first step is to finalize the design, including the size, shape, and logo customization. This stage ensures the tray meets specific client requirements.
- Material Selection
High-quality, food-grade silicone is carefully selected for its durability, flexibility, and safety. The material is BPA-free and meets all necessary safety standards.
- Mold Creation
A precise mold is created based on the customized design using advanced mold-making techniques. This step ensures the tray will produce perfectly shaped ice cubes every time.
- Injection Molding
Liquid Silicone Rubber (LSR) is injected into the mold under controlled conditions. The LSR is carefully cured to ensure optimal strength and flexibility of the final product.
- Curing and Cooling
After injection, the tray is cured at a specific temperature to solidify the silicone and improve its resilience. The tray is then cooled to maintain its shape and prevent deformation.
- Quality Control
Each tray undergoes rigorous quality checks to ensure it meets safety and performance standards. This includes inspecting for any defects, ensuring correct dimensions, and verifying material compliance.
- Packaging
Once the trays pass quality control, they are packed according to the client’s specifications, whether for bulk shipment or retail presentation.
- Shipping
Finally, the finished trays are carefully packaged and shipped to the customer, ensuring safe delivery and adherence to timelines.
Our Factory:
Our facility is equipped with cutting-edge manufacturing technology, including advanced CNC machining, Mirror EDM, and Slow-speed Wire Cut systems, complemented by 15 rubber compression molding presses and 2 high-performance LSR injection machines. We utilize specialized tools such as 3D projectors, sealing testers, and durometers to ensure precision in every stage of production. Our operations are further enhanced by capabilities in automatic screen printing, high-speed doming, die-cutting, and CNC machining, all managed by a dedicated quality control team. Certified to ISO 9001 and adhering to FDA standards, we uphold stringent quality assurance processes to deliver reliable, high-quality products tailored to meet specific customer needs, prioritizing safety and precision.
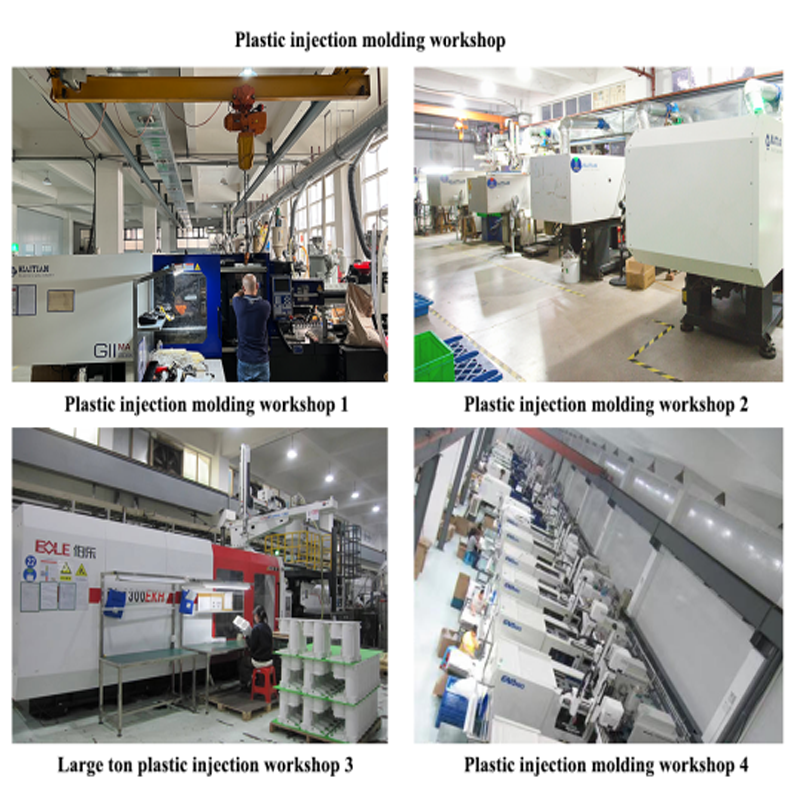
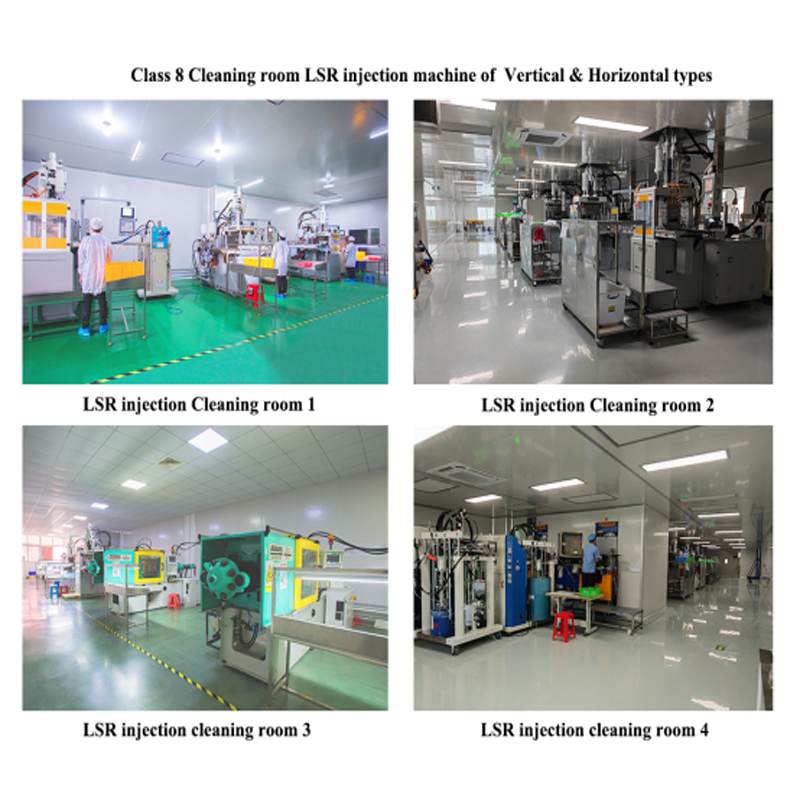