Overview:
Our Silicone Overmolding Baby Spoons are crafted with food-grade, BPA-free silicone overmolded onto a durable plastic or metal core. This ensures a soft, safe, and ergonomic feeding experience for babies. The seamless overmolding process guarantees durability and hygiene, while the gentle silicone tip is perfect for sensitive gums. With our custom and one-stop service, we provide personalized solutions for your baby product needs.
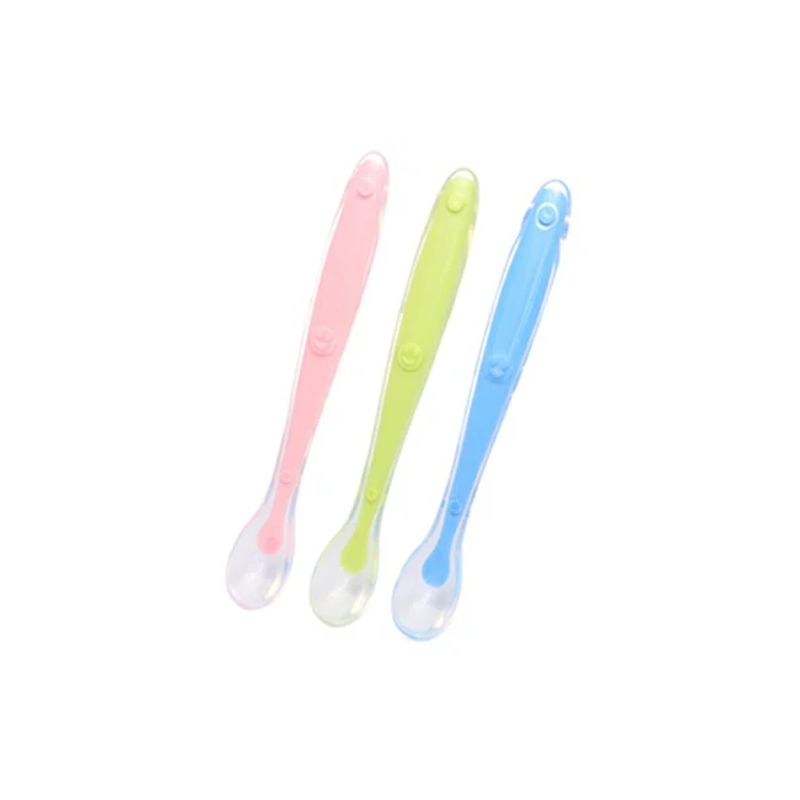
Characteristics:
Attribute | Details |
Place of Origin | Xiamen, China |
Material | Silicone |
Brand Name | OEM |
Color | Various colors |
Design | Custom |
OEM | Yes |
Delivery Time | 5-10 days |
MOQ | Small Order Can be Accepted |
Logo | Customized Logo Acceptable |
Packing | Customized Packing |
Sample | Available |
Benefits of Our Spoons:
- Customizable Design
- Temperature-Sensing Technology
- Variety of Colors
- Durable and Safe Material
- Quick Delivery & Customized Packing
Production Process:
- Design and Prototyping
The process begins with the design phase, where custom specifications, such as shape, size, and branding, are finalized. Prototypes are created to ensure the design meets functional and aesthetic requirements before mass production.
- Material Selection
Food-grade, BPA-free silicone is chosen for the overmolding process to ensure safety, durability, and ease of cleaning. The core material (often plastic or stainless steel) is selected based on strength, flexibility, and food safety standards.
- Injection Molding of the Core
The first step in the molding process involves creating the core component of the spoon, typically made of plastic or metal. This is done through injection molding, where the selected material is heated and injected into a mold to form the basic shape of the spoon.
- Silicone Overmolding
Once the core is cooled and solidified, the silicone overmolding process begins. The silicone material is heated and injected over the core to create a seamless bond. This step is crucial as it ensures that the silicone layer adheres securely to the core, providing durability, flexibility, and a soft, baby-friendly surface.
- Cooling and Curing
After overmolding, the spoons are cooled to solidify the silicone and ensure proper bonding with the core material. The silicone is then cured to enhance its strength and flexibility.
- Trimming and Finishing
Excess silicone around the edges is trimmed away to achieve the final shape and smooth finish. This step also includes any necessary post-processing to ensure the spoon is free of defects.
- Quality Control and Testing
Each spoon undergoes rigorous quality control checks to ensure it meets safety standards, is free from defects, and functions as intended. Testing includes checks for BPA-free certification, temperature resistance, and overall durability.
- Packaging
The final product is carefully packaged, with custom packing options available for branding. The spoons are then ready for shipment to customers or distributors.
Quality Assurance:
The Quality Control process for Silicone Overmolding Baby Spoons includes a series of rigorous checks to ensure safety and durability. Visual inspections using automated vision systems detect defects, while spectrophotometers and tensile testing machines verify the silicone meets food-grade and non-toxic standards. Thermal cycling machines test temperature resistance, and pull-off adhesion tests check the bond strength between silicone and the core. Hardness testing with durometers ensures the silicone is appropriately soft for babies. Functional testing simulates real-life use to assess ergonomics and safety. All products comply with ISO 9001 and baby care safety certifications, ensuring top-quality and infant-safe standards are met.
Our Factory:
We operate a fully equipped production facility with state-of-the-art plants and machinery to ensure top-quality output. Our mold-making capabilities include advanced CNC, Mirror EDM, EDM, and Slow-speed Wire Cut WC, along with other auxiliary equipment. The production lines feature 15 rubber compression machines and 2 LSR injection machines. To uphold high quality standards, we utilize 3D projectors, sealing testers, elasticity meters, durometers, and a skilled QC team. Additionally, our facility is outfitted with an AutoDryer Line, automatic screen printing machines, 3D measuring instruments, high-speed doming machines, die-cutting machines, and CNC machines. This blend of advanced equipment, automated processes, and strict quality control guarantees premium product standards.
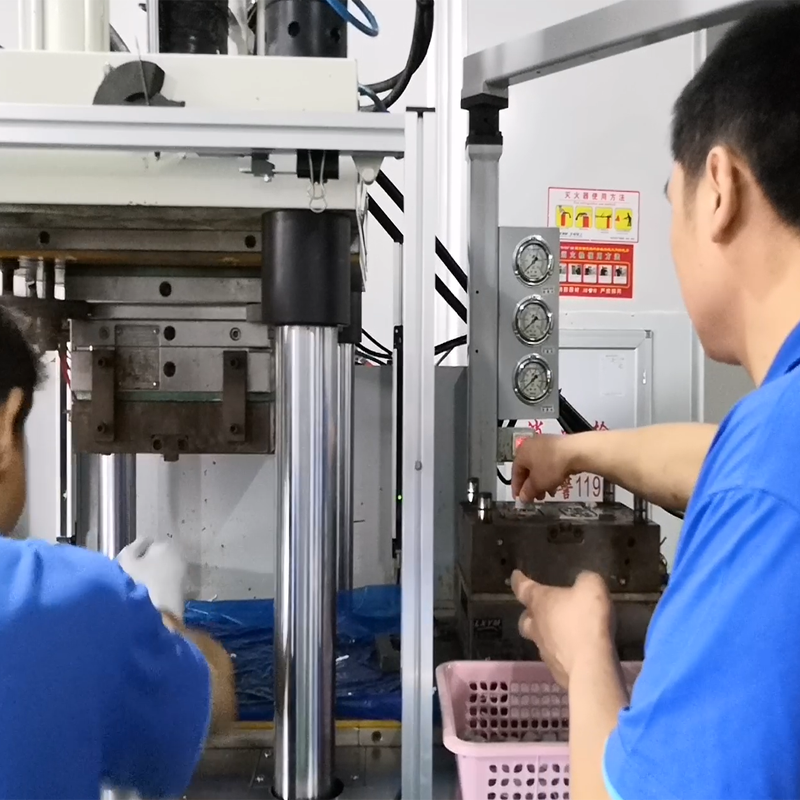