Description:
Our team of senior product designers offers comprehensive OEM services for Liquid Silicone Rubber Cups, encompassing design, prototyping, and contract manufacturing. We focus on delivering high-quality, safe silicone cups that meet stringent standards. After a meticulous secondary vulcanization process, our cups adhere to strict VOC, VOM, and FDA regulations, ensuring they are non-toxic, odorless, and safe for food contact. We provide extensive customization options—including material, size, design, functionality, structure, shape, color, logo, pattern, packaging, and labeling—empowering you to successfully realize your silicone projects for both personal and commercial use.
Details:
Specification | Details |
Material | Liquid Silicone Rubber / LFGB Silicone |
Process | Liquid Silicone Rubber Injection Molding / Laser Printing |
Logo Options | Custom Silk Screen / Laser Printing |
Design Features | Unbreakable drinking glasses with flexible shapes and utility |
Applications | Drinkware, Travel, Gifts, Advertising |
Production Process:
- Material Preparation: High-quality liquid silicone rubber is carefully measured and mixed to ensure the correct formulation, including additives for enhanced performance.
- Injection Molding: The prepared silicone mixture is injected into pre-heated molds using precision injection molding machines. This step ensures accurate shaping and consistency in the final product.
- Curing Process: The molded cups undergo a curing process, where they are subjected to controlled heat to facilitate vulcanization. This step solidifies the silicone, enhancing its durability and flexibility.
- Cooling and Demolding: After curing, the cups are allowed to cool before being removed from the molds. This process prevents deformation and maintains the integrity of the product.
- Quality Inspection: Each cup is subjected to rigorous quality control checks to ensure it meets safety and performance standards. This includes testing for defects, dimensions, and compliance with regulatory requirements.
- Finishing Touches: Final processes may include surface treatments, logo printing, or custom packaging, tailored to customer specifications.
- Packaging and Shipping: The finished products are packaged securely for transportation, ensuring they arrive at their destination in optimal condition.
Why Choose US?
– Tailored OEM Services: Our factory enthusiastically embraces OEM projects, delivering customized solutions designed to fulfill your specific requirements.
– Competitive Pricing: Operating our own silicone manufacturing facility allows us to provide exceptionally competitive pricing. By managing all production processes in-house, we ensure rigorous quality control at every stage.
– Comprehensive One-Stop Solution: We offer a full suite of services, from product development to large-scale production, enabling you to effectively bring your designs to market while minimizing costs.
– Quality Assurance: Our advanced quality inspection systems are designed to uphold the highest standards of product excellence. We take pride in delivering superior quality that is recognized and trusted by customers around the globe.
Factory Show:
Our factory spans 4,500 square meters and has over 20 years of OEM experience. Equipped with advanced machinery like Roders, Makino, Sodick, and YCM, we ensure top-tier production capabilities.
Utilizing cutting-edge equipment, we achieve micron-level precision in tool fabrication. Our tools, including ARBURG and Miltitech, allow us to produce ultra-precise components weighing as little as 0.02 grams and measuring down to 0.1 millimeters. Additionally, our ISO-certified Class 8 medical dust-free workshop provides a reliable environment for manufacturing medical device components, ensuring compliance with industry standards.
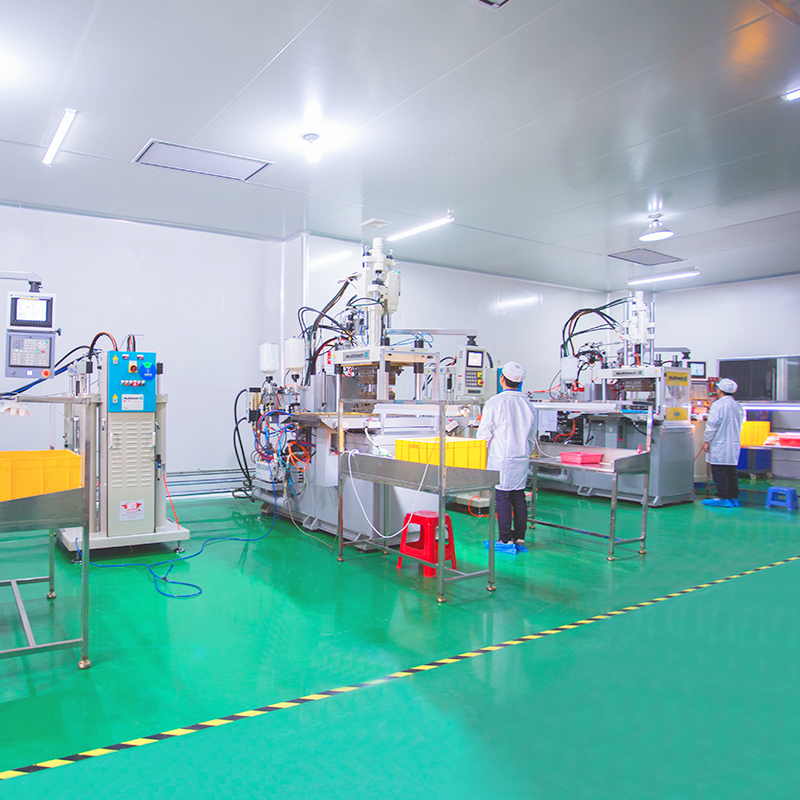
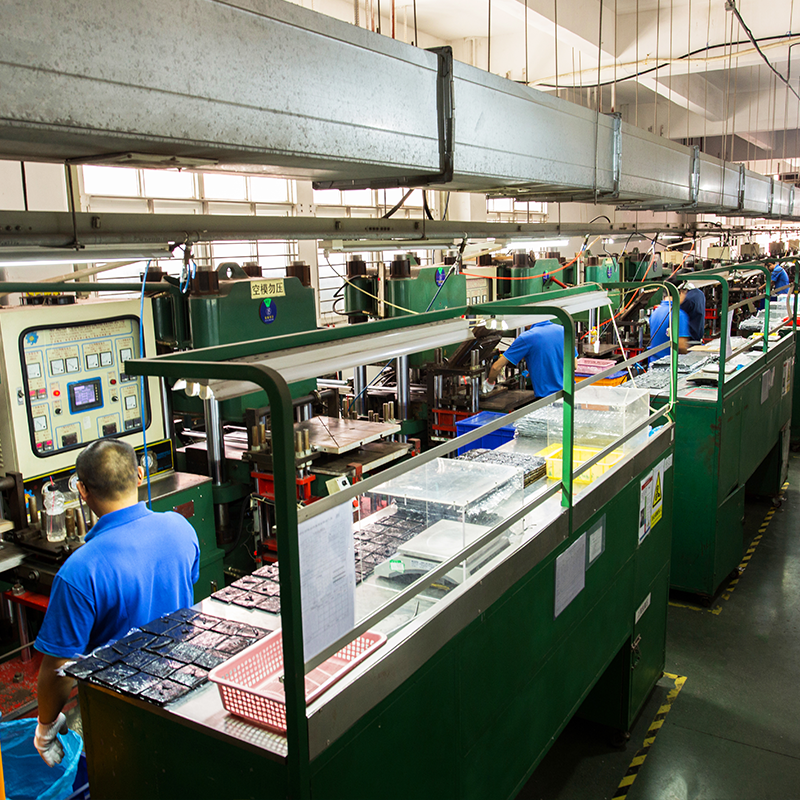