Overview:
Silicone O-rings excel in high-pressure sealing by deforming under compression, creating a robust barrier that prevents fluid leakage. Made from liquid silicone rubber using precision injection molding, these O-rings are available in durometers from 10 to 70 Shore A. This range ensures optimal control of elongation and softness, with 30 durometer O-rings offering balanced performance, and softer 10 and 20 durometer options providing flexibility. Customized for specific sealing needs, our O-rings ensure reliable and effective performance in various applications.
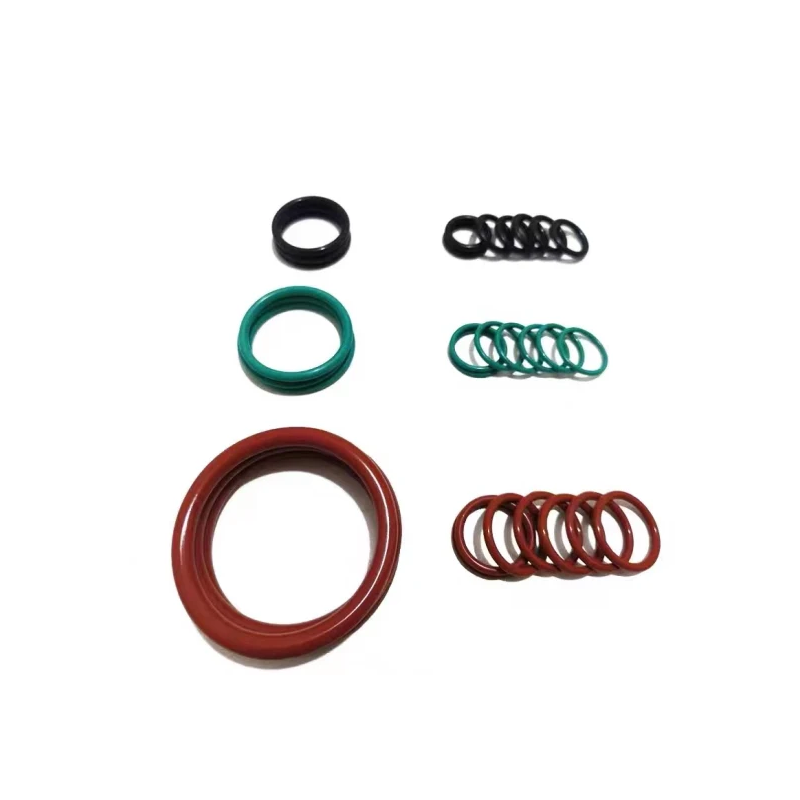
Features:
Attribute | Details |
Place of Origin | Xiamen, China |
Brand Name | OEM |
Product Name | O-Ring |
Material | Silicone Rubber |
Application | Industry |
Color | Customized Color |
Hardness | 20–90 Shore A |
MOQ | According To Your 3D Drawing |
OEM | Accepted |
Sample | Available |
Size | Custom Size |
Feature | Heat Resistance |
Advantages of Silicone O-Rings:
– Temperature Tolerance: Silicone O-rings perform well in both high and low temperatures.
– Compression Set Resistance: Exceptional resistance to compression set, maintaining seal integrity over time.
– Ozone and UV Stability: Outstanding stability against ozone and ultraviolet (UV) exposure.
– Oxidation Resistance: Superior resistance to oxidation, ensuring long-term durability.
– Water Sealing: Excellent capability for sealing against water ingress.
– Softness Options: Available in soft grades, including 10, 20, and 30 durometer Shore A, for tailored flexibility and performance.
The Manufacturing Processes of Silicone O-Rings
- Material Preparation: Silicone rubber is formulated and compounded with various additives to achieve the desired properties, such as flexibility, hardness, and temperature resistance.
- Molding: The silicone rubber is either injected into a mold or compression-molded to form the basic shape of the O-ring. Liquid silicone injection molding is commonly used for precise and high-volume production, where the rubber is injected into a heated mold to cure and take shape.
- Curing: The molded O-rings are then cured in an oven at high temperatures. This process, known as vulcanization, cross-links the silicone polymers to enhance their strength, durability, and elasticity.
- Trimming: After curing, excess material or flash is removed from the O-rings to ensure they meet the specified dimensions and have a clean, finished appearance.
- Inspection: Each O-ring undergoes thorough inspection to check for defects, verify dimensions, and ensure the quality of the product. This includes testing for properties such as hardness, elasticity, and visual appearance.
- Packaging: The inspected O-rings are then packaged according to customer specifications and prepared for shipment. Packaging can include bulk packaging or individual packaging depending on the order requirements.
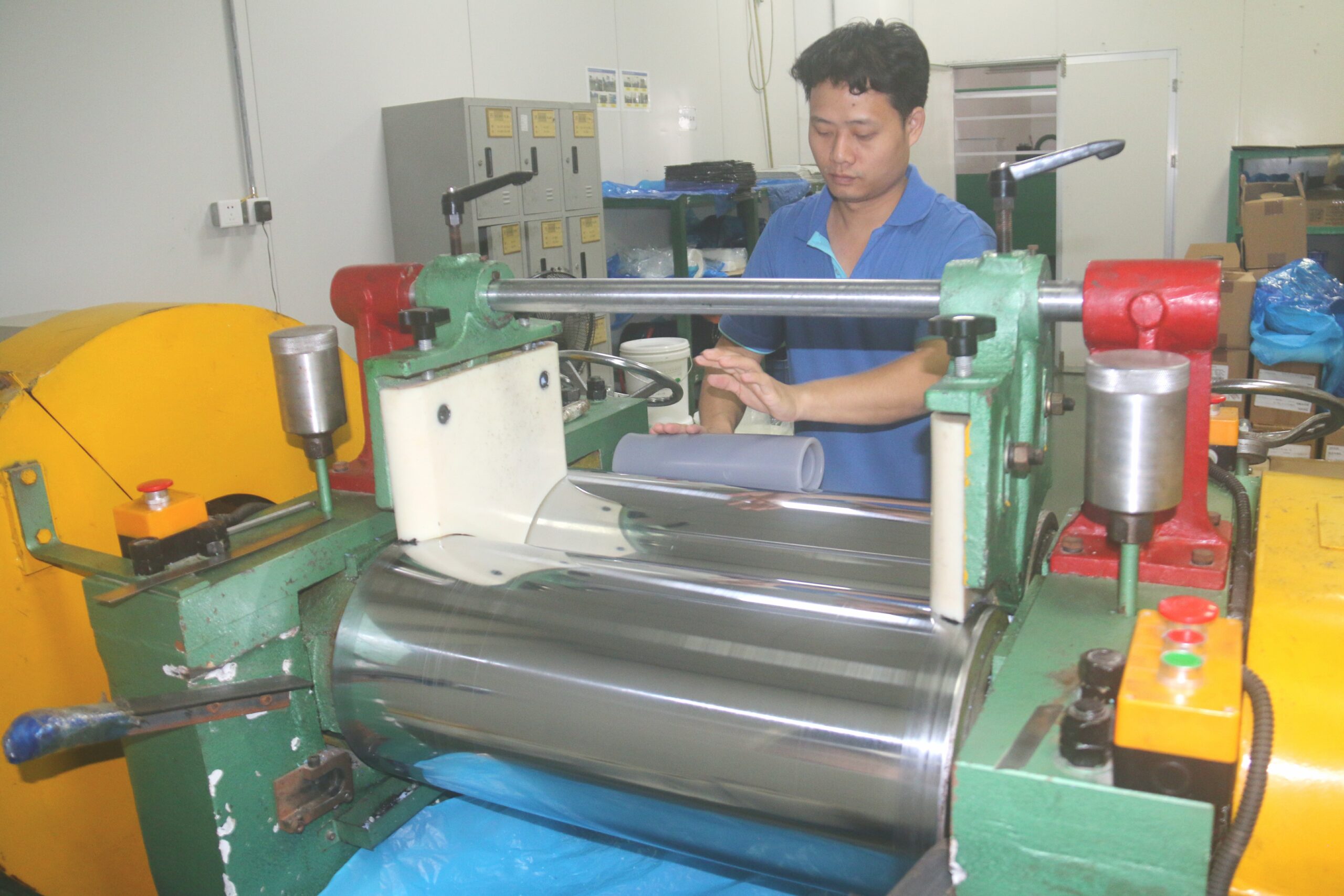
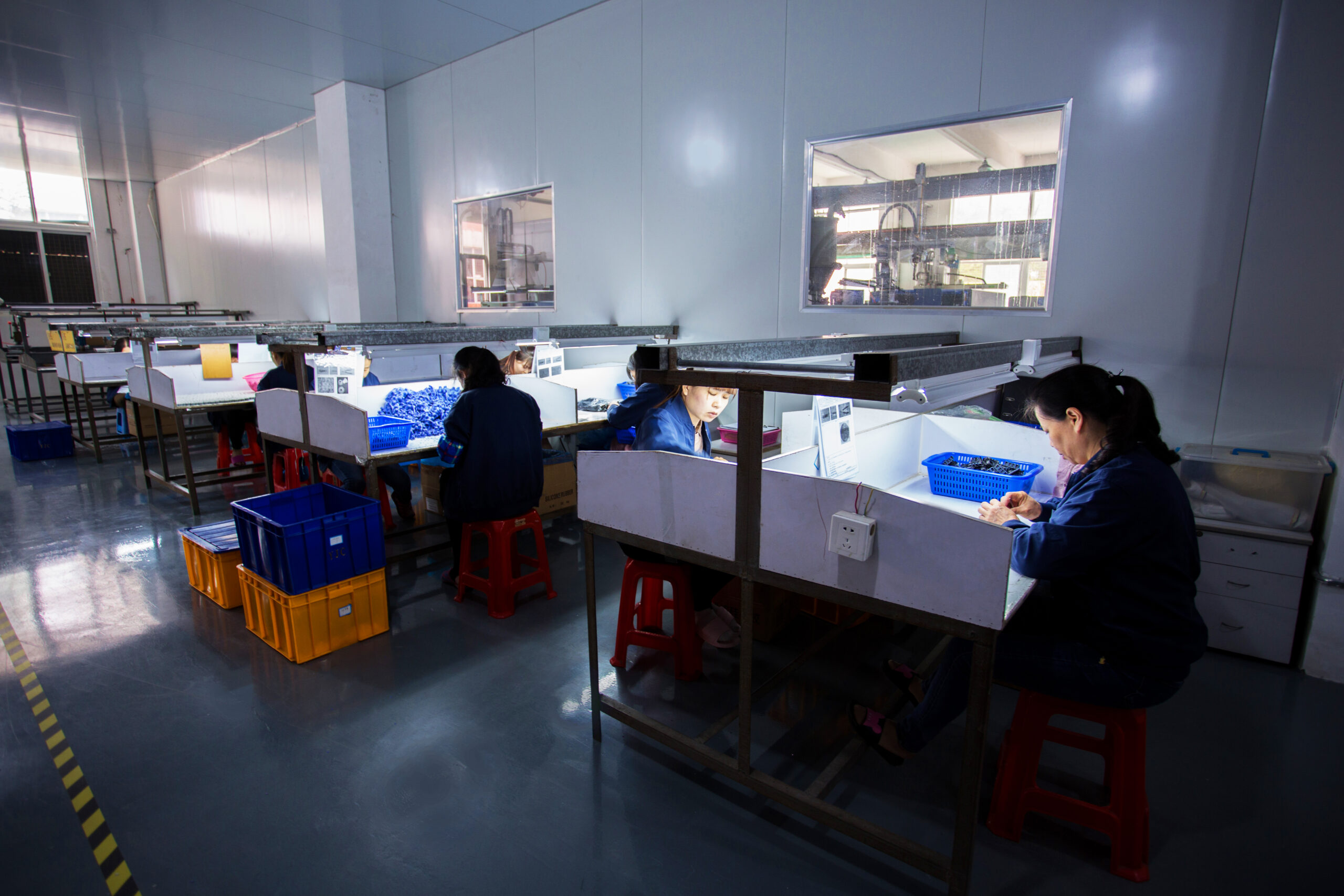